Currently, there is a trend for improvement and change programmes in the Norwegian oil and gas industry and the level of ambition to improve the way we operate is at an all-time high. Some companies put hundreds of millions, even up to billions of NOK, into development programs, digital roadmaps, digital transformation targets and so forth, but are we able to take these developments into good use?
Can we “future-proof” or modernise the way we work?
Or is the way we are working outdated despite all the ongoing initiatives to improve just that?
The system-requirements to run an oil and gas facility are complex. The multidiscipline competency and expertise required to maintain these system-requirements are vast. One of the major drivers to add to this complexity is the level of proprietary, 1-off solutions, many of which have been developed internally. This often results in a sub-optimal solution that is expensive to develop. In most cases this will also struggle to provide a long-term economic benefit compared to more off-the-shelf solutions. The proprietary properties in such systems also bring issues when you want to digitalise the systems. This could be related to incompatible communication protocols, old and unsupported operating systems and software in general. Another issue is the requirement for available resources at the plant for local support.
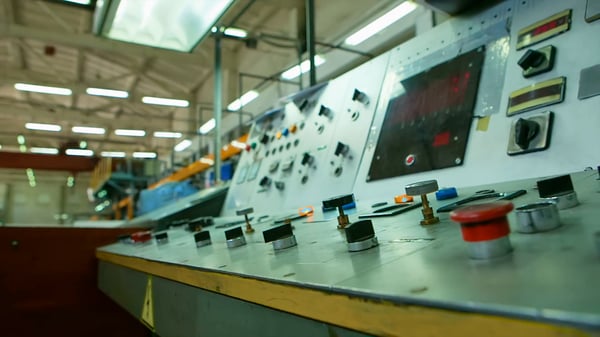
Image by: procinemastock
To prepare for growth, system-convergence, digitalisation and integration, you should choose a system that is as common as possible and has a long life-expectancy with continuous improvements and upgrades. A good example is from the automotive industry, where Tesla is purchasing SAT Nav from Google rather than developing and maintaining their own navigation system. On the other end you find manufacturers as BMW, Audi, Volvo, and similar, who all have the proprietary solutions. The difference between these two approaches will be having a fully functional vs. a sub-par functional solution, which is expensive both to develop and maintain. We have the concerns with technical solutions used in the oil and gas industry, which are often highly adapted for a specific use and expensive due to few customers/users.
Proprietary solutions can create a high risk for increased downtime and long recovery time if any incidents occur. This could be due to a lack of available resources with knowledge and competency on these systems, or lack of replacement hardware or software/configuration. Another risk is that maintenance personnel are reluctant to modify or change the systems, especially if the changes are implemented from a “top down” perspective that give an impression that the part of the organisation with mandate to implement change is lacking understanding of how the systems work - “The guys onshore”.
As long as you don’t have the workforce or “the people at the plant” onboard for change, it is very difficult to generate a lasting change. This is especially the case when the installed base is outdated and you want to implement both new technology and new ways of working, which could result in:
- Fear of putting the trust into hands of people at a remote location - performing critical changes on live systems at the facility.
- Fear of losing their jobs due to more automation, usage of robots or removing manual task.
- Poor utilisation of new technology and methods.
Is there anything to be gained from modernisation?
There is a great opportunity to gain common benefits if the industry collaborates to focus on their main business areas and share efforts to develop supporting functions and systems. This requires a more transparent mindset and may cause reluctance due to exposure of technological weaknesses and vulnerabilities between companies. The result of collaboration may lead to more robust and supported solutions that could gain better traction during change processes. Standardisation, knowledge, and understanding of new tools and methods will be key to achieving a digital transformation and a sustainable development for new ways of operating an oil and gas facility. This may build a foundation for more common and inter-functional technical solutions that are cheaper to install, maintain, and modify. This will be possible if we achieve compatibility between various systems, e.g. between control systems to facilitate for multifield control rooms, or common protocols for communication to have all data available on a common platform. You will still need to divide certain areas of your networks and segregate some areas for safety and process integrity purposes, but the data will be more available to flow where you want it.
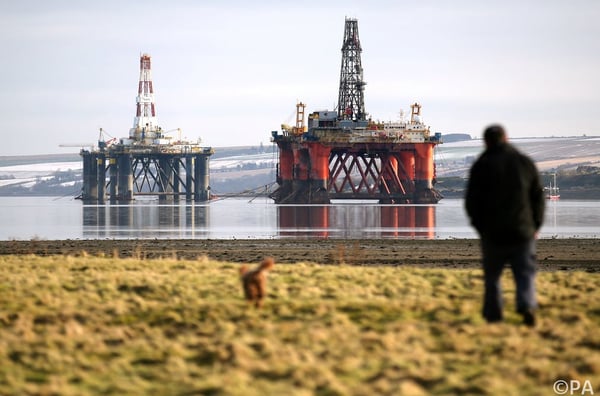
How do we modernise the way we work?
The modernisation of the technical solutions and the way we operate and maintain them, will be highly dependent on the alignment between change processes and the user’s will and interest to adopt the new solutions. The new solutions should be fit for purpose, developed through collaboration, well designed and implemented along with the users. The digital initiatives need to improve the way we work and not be perceived as a hassle and a trendy thing that will disappear in the near future.