We all know how a small, trivial thing can escalate and turn into a big problem. A tiny decimal point can make all the difference. Consequently, it’s important to know what can go wrong if even a small variable is set incorrectly, and of course how to detect if there are any potential problems that can develop within our control system.

How do I detect potential problems?
A typical indicator of an existing control system issue regarding the selected tuning parameters for a controller, is if controllers are set to operate in manual mode over a longer period of time. This usually means that the parameters selected for the controller are too aggressive and needs a more conservative adjustment. Suppose that a process plant has several controllers operating in manual; in that case, it is likely to have a negative effect on the plant production, as the control room operator will have to use more time on operating controllers that should be operating in auto mode. This is taking unnecessary time from the operator, which otherwise, could have been spent on other improvements on the process plant.
Another indicator of a control system issue is if the process is oscillating, meaning there are many high fluctuations in the process over time. All processes are oscillating to some extent, but good tuning parameters will contribute to making the oscillations as small as possible. If your plant has frequently triggered alarms due to fluctuations in the processing facility, the controllers may be in need of a new set of tuning parameters.
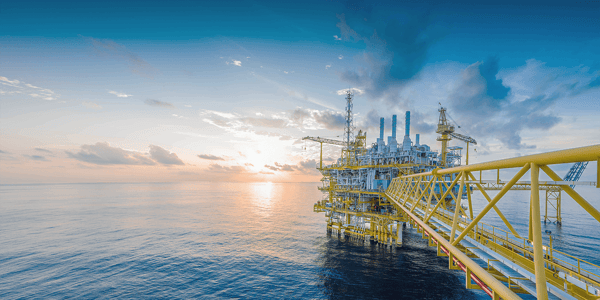
Why is it important that these problems don’t escalate?
A problem with the control system can, in worst case, lead to an unplanned shutdown. A less serious consequence of poor control is unnecessary maintenance. A poorly controlled process is likely to be oscillating more, and the mechanical elements associated with moving a valve or damper will wear out faster. Increased production costs are also associated with a poorly controlled process due to higher energy consumption and feedstock consumption. Another problem with poor controller tunings is when controllers are operated in manual over time. When controllers are set to manual, the operator needs to monitor and spend time operating the controller. Lastly, a result of not utilising optimal parameters, is possible loss of production.
In a more stable production environment, the quality will be better, and the quality of the product will be the same regardless of when it was produced.
How a small problem can lead to shutdown
In our example, a production facility had problems with oscillations in a distillation column, leading to unplanned shutdowns. For a long time, the problem was thought to be within the distillation column, and several approaches to fix the problem within the distillation column were attempted, but nothing worked. However, upon closer analysis and looking at the entire process while considering the process dynamics, they discovered that the level in a reboiler, located in a column upstream of the distillation column, was oscillating. The oscillating level in the reboiler caused fluctuations in the feed stream to the distillation column, which in turn caused the oscillations in the distillation column. After an investigation of the tuning parameters set for the level-controller in the reboiler, it was found that the reboiler's level-oscillations were caused by poor parameters set for this level controller. New tuning parameters were provided for the level-controller in the reboiler, and the problem was solved. Tuning this one controller meant increasing uptime, production, and reducing wear and tear on the equipment.
What can I do about my control system problems?
One thing you can do to avoid these problems or correct the problem if it is already causing trouble, is ensuring that the parameters selected for the controllers have been selected through a systematic approach, taking the process dynamics into consideration. Considering process dynamics includes taking into account how the surrounding loops are affecting each other. This ensures an optimised process and will, in most cases, lead to increased uptime and could increase production by as much as 5-10%!